Běhoun, Nárazník, Bočnice, Patní pásek, Patka pneumatiky, Patní lanko, Kostra pláště - radiální a diagonální konstrukce, vnitřní guma
Značení pneumatik a disků
Značení pneumatik, Značení disků
Úkol pneumatiky, Radiální pružnost pneumatiky, Obvodová pružnost pneumatiky, Boční pružnost pneumatiky
Princip přenosu sil
Faktory ovlivňující velikost adhezní síly, Vliv povrchu vozovky na součinitel adheze, Vliv vlastností povrchu pneumatiky na součinitel adheze, Vliv výšky vzorku běhounu a materiálu běhounu na součinitel adheze, Vliv měrného tlaku ve stopě na součinitel adheze, Vliv rychlosti jízdy na koeficient adheze
Konstrukce pneumatik
Hlavním úkolem pneumatiky je přenášet síly, které pohánějí, brzdí a vedou vozidlo a nést určitou zátěž. Při plnění tohoto hlavního úkolu musí být ještě pneumatika schopná absorbovat nerovnosti na vozovkách s různým charakterem povrchu a zajišťovat při tom hladkou a bezpečnou jízdu bez jakýchkoliv vibrací na vozovkách s kvalitním, minimálně hrbolatým povrchem. Tyto dva požadavky jsou navzájem protichůdné, protože absorbování nerovností vyžaduje ohebnost a pružnost pneumatiky, zatímco základním předpokladem pro hladkou jízdu s konstantní světlou výškou vozu na ploché a hladké vozovce je konstantní účinný rozměr pneumatiky. Při jízdě pneumatiky na vozovce s určitou výškou vodního filmu musí být zaručen bezpečný odvod vody z míst, kde se pneumatika stýká s vozovkou. Toto lze zaručit, jen pokud je běhoun pneumatiky vybaven vzorkem s dostatečným počtem a šířkou drážek. Čím je však větší poměr celkové plochy drážek ku celkové ploše vzorku, tím se zvětšuje náchylnost pneumatiky k opotřebení a zvyšuje se hlučnost pneumatiky při jízdě.Při volbě tvrdosti směsi pro výrobu jednotlivých konstrukčních částí pneumatiky proti sobě stojí tvrdá směs zaručující nízké opotřebení, boční stabilitu a nízký valivý odpor a měkká směs přinášející lepší adhezní vlastnosti a účinnější absorpci nerovností vozovky.O vzájemné vyvážení těchto a mnoha dalších protichůdných vlastností pneumatiky se starají různé materiálové, tvarové a rozměrové variace jednotlivých konstrukčních prvků pneumatiky.
Konstrukční prvky pneumatiky
Plášť pneumatiky se skládá z těchto hlavních strukturních částí: běhoun (1), vzorek pozitivní (2), vzorek negativní - drážka (3), rameno pneumatiky (4), bočnice (5), kostra pneumatiky a patka pláště (6), patní lano (7), nárazník (8), PA nárazník a praporek (9),
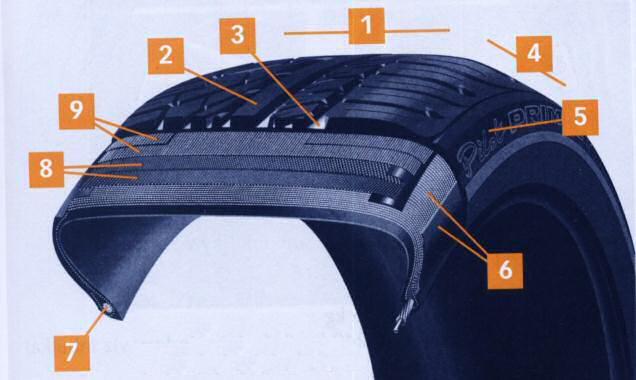
Běhoun je část pláště opatřená vzorkem a zajišťující styk kola s vozovkou.Jeho tloušťka má vliv na zahřívání pneumatiky, a z toho důvodu by měl být co nejtenčí. V praxi se tedy tloušťka běhounu volí tak, že vzorek s drážkou tvoří přibližně 80% a hmota asi 20%. To však neplatí u plášťů pro nákladní vozidla, u nichž je většinou běhoun konstruován pro možnost dalšího prořezání drážek vzorku. U plášťů pro osobní vozy je prořezávání zakázáno. Vzorek běhounu se někdy nazývá dezén. V praxi může být plášť pneumatiky opatřen dvouvrstvým běhounem. Vrchní vrstva běhounu má vysokou odolnost proti opotřebení a spodní vrstva běhounu je vyrobena tak, aby měla co nejmenší hysterezní ztráty při dynamickém namáhání. Nízké hysterezní ztráty znamenají nízké teplotní namáhání pneumatiky.Funkce: Vnější část – životnost a dostatečná adheze s vozovkou; Vnitřní část – snížení valivého odporu, ochrana kostry a nárazníku před mechanickým poškozením. Právě dostatečná adheze na všech druzích povrchů a za všech klimatických podmínek je dominantním úkolem běhounu pneumatiky. Rozmístění a tvar drážek a segmentů běhounu má své opodstatnění a je výsledkem pečlivého zkoumání a dlouhodobého vývoje podpořeného množstvím praktických zkoušek a testů.
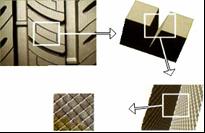
Vnější zóna (1) je nejvíce namáhána při manévrování. Je tvořena tuhými, maximálně pevnými bloky, jejichž úkolem je zabezpečit co nejlepší jízdní stabilitu vozidla a přesné a bezpečné ovládání. Vnitřní zóna pneumatiky (2) má díky příčným drážkám výrazně posilující účinek záběru na sněhu a je konstruována tak, aby dokázala zajistit dostatečný odvod vody při jízdě na mokrých vozovkách. Čtyři široké obvodové drážky (3) mají za úkol zajistit dostatečné držení směru jízdy a jsou důležité při odvodu vody ze styčné plochy pneumatiky s vozovkou. Příčné drážky (4) jsou umístěny ve výrazně tangenciálním směru ke směru jízdy. Mají za úkol efektivně odvádět vodu při jízdě na mokré vozovce a starat se o co nejlepší záběr na sněhu. Technologie nestejně širokých bloků ve vnitřní i ve vnější zóně (5) částečně eliminuje hluk vznikající při odvalování pneumatiky. Husté lamelování (6) zvyšuje záběrovou a brzdící schopnost pneumatiky. Při akceleraci nebo brzdění dojde v místě styku s vozovkou k rozevření lamel, a vznikne tak velké množství záběrových hran, které přispívá k lepším adhezním schopnostem pneumatiky hlavně na mokré a zledovatělé vozovce. Hlavní význam přítomnosti lamel při jízdě na mokré vozovce spočívá v tom, že při rozevření lamel se do vzniklých dutin může dostat voda, a tím se zmenšuje množství vody, které je nutno odvézt ze styčné plochy pneumatiky s vozovkou. Při přenosu bočních sil se lamely jednoho bloku do sebe zaklesnou a nerozevřou se. Vznikne tak blok s vyšší tuhostí, který je příčinou lepší boční stability a nižšího opotřebení. Množství, tvar a rozmístění lamel má významný vliv na vlastnosti pneumatiky. Na obrázku je zobrazeno revoluční patentované řešení lamel Michelin. Po rozevření lamely zde zachytávají o vozovku vnitřní plošky lamel, jejichž povrch je uměle zdrsněn.
Nárazník tvoří přechod mezi běhounem a kostrou pláště. Jeho úkolem je stabilizovat běhoun v obvodovém směru a zvyšovat odolnost pláště proti průrazu. U radiálních pneumatik zachycuje nárazník prakticky veškerá namáhání v obvodovém směru běhounové části pneumatiky. U nákladních automobilů se používají v průměru tři až čtyři, u osobních pak většinou dvě nárazníkové vrstvy. Radiální pneumatiky mají dnes již téměř výhradně nárazník prokládaný ocelovým kordem (pneumatiky Steel).
Polyamidový (PA) nárazník je umístěn nad nárazníkem. Někdy se označuje též jako překrývací nárazník. Jeho kordy jsou v pneumatice uložené ve směru odvalování (úhel 0°). Nad nárazníkem bývá obvykle položen v jedné nebo ve dvou vrstvách. Materiál: Pogumovaný polyamidový kord. Funkce: Díky vyztužení spodní části běhounu umožňuje dosažení velmi vysokých rychlostí bez obvodové deformace pneumatiky. Má vliv na snížení valivého odporu a zlepšení jízdního komfortu.
Nárazník - materiál: Pogumovaný ocelový kord s kordovými vlákny uloženými ke směru odvalování pod malým úhlem (15 - 20°). Funkce: Zajišťuje odpovídající životnost pneumatiky, stabilizuje běhoun, předchází hlubokému poškození kostry pláště, jeho konstrukce má veliký vliv na snížení valivého odporu.
Bočnice je vyrobena z přírodního kaučuku, který je časově odolný, pevný v tahu a odolný proti vzniku a růstu trhlin. Zajišťuje ochranu kostry před vnějšími vlivy. Nepodléhá stárnutí a vydrží mnohonásobný ohyb. Spojuje patky pláště s běhounem. Stárnutí je u bočnice způsobeno vlivem kyslíku obsaženém ve vzduchu. Stárnutí je zabráněno přidáváním antioxidantů a antiozonantů do kaučukové směsi bočnice. Tyto přísady na sebe vážou atmosferický kyslík a ozón. Na bočnici najdeme vyznačeny všechny potřebné údaje identifikující daný plášť.
Ochranný patní pásek je vyroben ze syntetického kaučuku. Jeho úkolem je předcházet erozi patky pláště v místě styku s ráfkem a zabezpečovat těsnost a pevné spojení s ráfkem.
Výztužný pásek má za úkol zpevňovat a stabilizovat přechodovou oblast mezi patkou pláště a boční stěnou. Je vyroben z pogumovaných nylonových nebo aramidových kordů.
Patka pláště zesiluje boční část pláště, která v oblasti patních lan dosedá na opěrné plochy ráfku disků kol. Vlivem tlaku vzduchu v pneumatice je patka pláště přitlačována na ráfky. Patka má za úkol přenášet všechny boční síly vznikající mezi ráfkem a pláštěm a nesmí dovolit únik vzduchu v oblasti opěrných ploch ráfku.
Jádro patky je vyrobeno ze syntetického kaučuku. V pneumatice má za úkol zajišťovat postupný přechod z oblasti patky, která se vyznačuje vysokou tuhostí, do elastické oblasti bočnic pneumatiky. Zabezpečuje velkou boční tuhost pláště a dokonalý přenos příčných sil. Jádro patky obsahuje přídavné textilní nebo ocelové kordové výztuže, které mají za úkol zvýšit ohybovou tuhost patky v nadpatkové části pláště. Díky této zvýšené tuhosti je zmírněno vydouvání pláště v oblasti dosedacích ploch ráfku, a je tak zabráněno možnosti sesmýknutí pneumatiky z disku kola při působení bočních sil.
Patní lanko je vyrobeno z pogumovaného svazku vysokopevnostních ocelových drátů. Díky třecím silám vznikajícím mezi pryžovými povrchy vyztužuje patku v obvodovém směru, čímž zaručuje správné a bezpečné usazení pláště na ráfku a těsnost spojení pneumatiky s ráfkem. Okolo patního lanka jsou zakotveny kordové vložky kostry.
Kostra pláště je základní část pláště složená z vložek tvořených kordovými vlákny. Vložky jsou zakotveny kolem patních lan. Její stavba a složení určují základní vlastnosti pláště. Velmi důležitou částí kostry jsou vlastní kordová vlákna, která jsou během procesu pogumování pogumována. Hlavním úkolem kostry je zabezpečit přenos tažného momentu a současně nedovolit změnu tvaru pneumatiky. Dále pak předchází roztržení pneumatiky při pracovním tlaku.
V průběhu vývoje pneumatik se změnil jednak systém kladení vláken ( od křížené tkaniny v dávné historii k paralelnímu kladení netkaných kordových vláken v současnosti), a jednak materiál. Vývojově prvním používaným materiálem byl irský len, později nahrazený bavlnou. U těchto materiálů se však projevovaly nectnosti přírodních materiálů (nehomogenita, závislost na vlhkosti apod.), a proto se s příchodem umělých vláken a ocelového kordu od jejich dalšího používání upustilo. Stále se však u některých typů pneumatik používá smluvní vyjádření pevnosti kostry a nosnosti pneumatiky, tzv. Ply Rating (PR), kde číslo přidružené k PR značí, z kolika vrstev bavlněného kordu by musel být plášť zhotoven, aby měl stejnou nosnost jako plášť označený příslušnou hodnotou PR.
Dnes se tedy k výrobě vložek pro kostru pneumatiky používají nejčastěji: raylon (obchodní název pro umělé hedvábí), polyesterový kord, ocelový kord, polyamidový kord, kevlarový kord (nové syntetické vlákno používané u speciálních, např. sportovních plášťů).
V části věnované nárazníku jsme již narazili na označení plášťů Steel. U nich je tedy ocelovým kordem vyztužen pouze nárazník. U plášťů All Steel je i samotná kostra pláště tvořena ocelovým kordem.
Podle uspořádání kordových vložek vkostře se pláště dělí na: radiální, diagonální a pláště smíšené konstrukce.
Diagonální pneumatika má kordové vložky kladeny na sebe tak, že kordy vždy dvou na sobě ležících vložek se navzájem kříží pod úhlem 30° - 40°. Tyto pláště nemívají nárazník, protože zachycení obvodových sil zajišťuje právě diagonální orientace kordových vláken v kostře. U diagonálního pláště se při zatížení a následné deformaci kordová vlákna neprodlužují, ale posouvají a namáhají pryž mezi nimi na střih. Tím dochází k většímu vývinu tepla, čemuž odpovídá známý fakt, že se diagonální pneumatika během provozu oproti radiální pneumatice více zahřívá.
Radiální pneumatika má kordy ve všech kordových vložkách kostry vedeny od patky k patce kolmo na rovinu rotace kola. Boční síly zde zachycují kordy v kordových vložkách kostry a o obvodové síly se stará nárazník, v jehož jednotlivých vrstvách jsou kordy kladeny téměř kolmo na kordy kostry.
Srovnání diagonální a radiální konstrukce kostry: Ve srovnání s diagonálními zachycují radiální pneumatiky lépe boční síly, což způsobuje, že při zatížení boční silou zůstává větší část radiálního pláště ve styku s vozovkou. Další výhodou radiální konstrukce je, že díky nárazníku mají větší obvodovou tuhost pláště. Díky těmto dvěma výhodám vynikají radiální pláště lepší adhezí, nižším opotřebením, větší odolností proti průrazu a menším valivým odporem. Jejich nevýhodou jsou naopak větší náklady na výrobu, větší choulostivost na špatné nahuštění, a větší hlučnost při jízdě na vozovce s nerovnostmi. Navzdory těmto nevýhodám se dnes u pneumatik pro osobní automobily již prakticky stoprocentně používají pláště radiální konstrukce. Výjimku tvoří pláště používané u zemědělské mechanizace a především pak u zemních strojů. Pro ně je charakteristické, že se pohybují malými rychlostmi po nerovných površích a přenášejí velké boční a obvodové síly. Diagonální plášť je zde vhodnější, jelikož zde působí jako pružící a částečně i tlumící jednotka bočních a obvodových sil. Nestabilní chování vozidla při působení těchto sil díky malým obvodovým rychlostem kol téměř neovlivní bezpečnost jízdy.
Vnitřní guma má za úkol zabránit úniku vzduchu z prostoru uvnitř pláště. Plní roli duše v bezdušových pneumatikách. Jako materiál pro výrobu vnitřní gumy slouží butylový kaučuk.
Značení pneumatik a disků
Značení pneumatik
Plášť pneumatiky slouží jednak jako součást umožňující přenos sil mezi vozidlem a vozovkou a jednak jako nosič důležitých údajů obsahujících informaci o jeho rozměrech, konstrukci, výrobci a spoustě dalších vlastností. Některé údaje jsou potřebné pro koncového uživatele, jiné ocení prodejce nebo technik, další jsou nepostradatelné v oblasti výroby a skladování. Způsob značení a vysvětlení jednotlivých údajů můžeme vidět na pneumatice Pirelli.
Profilové číslo udává procentuální poměr šířky pláště ku jeho výšce.
Index nosnosti neboli Load Index (LI) je číslo určující maximální nosnost pneumatiky při určité rychlosti dané rychlostním indexem za specifických podmínek. Hmotnostní hodnoty přiřazené k jednotlivým indexům nosnosti jsou uvedeny v sekci užitečné informace. Na pneumatice může být vyznačena i odpovídající nosnost při alternativní vyšší rychlosti. Takovýto údaj bude uveden v kroužku.
Index rychlosti neboli Speed Symbol (SS) představuje maximální rychlost, při které dokáže pneumatika unést hmotnost určenou indexem nosnosti za specifických podmínek. Hodnoty rychlosti odpovídající jednotlivým rychlostním indexům jsou zobrazeny v sekci užitečné informace.
Počet vložek v běhounu a v bočnici nám udává počet kordových vrstev umístěných v běhounu a bočnici a specifikuje druhy kordu, které byly při výrobě pláště použity.
Bezdušové provedení je u pneumatiky označeno nápisem TUBELESS nebo písmeny TL. Naproti tomu TUBE TYPE označuje pneumatiku, kterou je nutno používat s duší.
Datum výroby je značeno třemi nebo čtyřmi čísly, z nichž první dvojčíslí označuje kolikátý týden v roce byla pneumatika vyrobena a zbylá čísla značí rok výroby.
Údaje požadované pro USA jsou TREADWEAR (značí odolnost běhounu proti opotřebení v procentech), TRACTION (označuje třídu součinitele adheze pneumatiky), TEMPERATURE (symbolizuje odolnost pneumatiky proti dynamickému namáhání). TRACTION i TEMPERATURE může nabývat hodnot A,B nebo C.
Označení M+S značí pneumatiku vhodnou pro užívání v zimním období. U pneumatiky označené nápisem REGROOVABLE je možné prořezávat běhoun z důvodu prohloubení drážek ve vzorku. REGUMERAT nebo RETREAD značí protektorovanou pneumatiku.
OZNAČENÍ DOJEZDOVÝCH PNEUMATIK U VÝROBCŮ
RFT - BRIDGESTONE - (Run Flat Technology)
SSR, CSR - CONTINENTAL - (Self Supporting Runflate)
DSST, ROF - DUNLOP - (Dunlop Self Supporting Technology)
RFT - FIRESTONE - (Run Flat Technology)
EMT, ROF - GOODYEAR - (Run On Flat)
ZP - MICHELIN (Zero Pressure)
RFT - PIRELLI - (Run Flat Technology)
ZPS - YOKOHAMA - (Zero Pressure System)
XRP - KUMHO - (eXtended Runflat Perfomance).
HRS - HANKOOK
DALŠÍ ZKRATKY POUŽÍVANÉ RŮZNÝMI VÝROBCI PNEUMATIK
FR, FP, RPB, MFS, ML - Zkratky označující pneumatiky s ochranou ráfku.
XL, RF, REINF - Zkratky eXtra Load a ReinForced označují zesílenou pneumatiku.
ZR - Označuje speciální konstrukci pneumatiky určenou pro rychlosti nad 240km/h.
M+S - Mud + Snow (bláto + sníh) používá se k označení zimních nebo celoročních pneumatik.
C - Pneumatiky pro užitkové (lehké nákladní) vozy.
HP - výkonné pneumatiky (High Performace).
UHP - vysoce výkonné pneumatiky (Ultra High Performace).
AO - Pneumatika homologovaná pro Audi.
N0 - Pneumatika homologovaná pro Porsche.
N1 - Pneumatika homologovaná pro Porsche.
MO - Pneumatika homologovaná pro Mercedes.
J - Pneumatika homologovaná pro Jaguar.
* - Pneumatika homologovaná pro BMW.
REGUMERAT, RETREAD, REMIX - protektorovaná pneumatika.
REGROOVABLE - možnost prořezání dezénu, u pneumatik bez tohoto označení je zakázáno dezén prořezávat!
OWL - Outlined White Lettering - bílý nápis na bočnici.
ROWL - Bílý nápis na bočnici
OWT - Bílý nápis na bočnici.
RWL - Raised White Letter - bílý nápis na bočnici.
RBT - Vystouplé černé písmo.
BLT - Černé písmo na bočnici.
RBL - Vystouplá písmena bočnice.
S/T - Sport Truck.
A/T - All Terrain - univerzální pneu pro všechny typy terénu.
A/S - All Season. - celoroční.
M/T - Mud Terrain - pneumatiky do blátivého terénu.
H/P - Highway Performace - dálniční provedení.
H/T - Highway Terrain - provedení pro dálnici i terén.
RHD - Right Hand Drive - pravostrané řízení.
DALŠÍ ZKRATKY POUŽÍVANÉ PRO OZAČENÍ MOTOCYKLOVÝCH PNEUMATIK
M/C - MotorCycle - motocyklové pneumatiky.
F - Front - přední pneumatika.
R - Rear - zadní pneumatika.
SW - Slim White Sidewall - tenký bílý proužek na bočnici.
WW - White Wall - bílá bočnice.
WWW - Wide White Wall - široká bílá bočnice.
NWS - Narrow White Stripe - tenký bílý proužek na bočnici.
RF nebo REINF - Reinforced - zesílená verze.
MBS - Metzeler Belt System - speciální konstrukce výrobce Metzeler pneumatiky pro silné motocykly.
SLICK - označení pneumatik pro závodní použití.
NHS - označení pneumatik pro závodní použítí.
Značení disků
Ráfek tvoří společně s hlavou a diskem, hvězdicí nebo dráty kolo automobilu. Pomocí hlavy je kolo upevněno k nápravě, na ráfku je uložena pneumatika a disk, hvězdice nebo dráty slouží ke spojení hlavy a ráfku. Ráfky mohou být ploché nebo prohloubené, jednodílné nebo vícedílné. Pro provoz osobních automobilů se používají výhradně ráfky jednodílné a prohloubené. Tyto ráfky jsou nerozebíratelně spojeny s diskem, nebo hvězdicí nýtováním, nebo svařováním, nebo jsou s příslušnými částmi odlity či vykovány vcelku.
Každý ráfek můžeme definovat řadou údajů. Nejdůležitější jsou však údaje o šířce ráfku a průměru ráfku. Tyto údaje můžeme vyčíst z normalizovaného značení ráfku, které je uvedeno v následujícím příkladě.
4 J x 15 H
Číslo 4 označuje šířku ráfku v anglických palcích. Písmeno J označuje tvar okraje ramena ráfku. Písmenko x slouží jako oddělovací znaménko. Číslo 15 značí průměr ráfku v anglických palcích v místě dosednutí patek pláště na ráfek. Písmeno H informuje o přítomnosti bezpečnostního převýšení na vnějším rameni ráfku, označení H2 značí bezpečnostní převýšení na obou stranách. Standardně bývá bezpečnostní převýšení oblé. V případě, že by převýšení bylo ploché, bylo by v označení ráfku použito před písmenkem H písmenko F. Písmenko C značí kombinované převýšení – ploché na vnějším a oblé na vnitřním rameni.
U ráfků pro bezdušové pneumatiky musí být na koncích ramen blíže k prohloubení provedeno po obvodu určité bezpečnostní převýšení. Tvar převýšení může být oblý nebo plochý. Účelem převýšení je zabránit, zejména při jízdě zatáčkou, vtlačování patek pláště vlivem boční síly do prohloubení.
Dalším důležitým rozměrem ráfku je hodnota ET. ET (z němčiny einpresstiefe), česky zális, je udávaný v milimetrech. Je to vzdálenost dosedací plochy kola od pomyslné roviny dělící šířku kola na jednu polovinu. Tato definice se těžko představuje, a proto je lepší říci, že se jedná o to, jak hluboko se zasune kolo ke středu vozu. Čím větší je hodnota ET, tím je menší rozchod kol. Hodnota u většiny kol pro evropské vozy se pohybuje okolo 35 mm. Hodnotu ET můžeme zmenšovat (zvětšuje se tudíž rozchod kol) použitím distančních podložek a dlouhých šroubů.
Technologie výroby pneumatik
Technologicky je možné výrobu plášťů popsat jako několik vedle sebe probíhajících samostatných operací, které se potkávají až při tzv. konfekci. Je to vlastní příprava kaučukových směsí, pogumovaného kordu, výroba běhounů a bočnic, výroba patních lan a nárazníků. Zmíněná konfekce je potom zkompletování všech komponent. Jejím produktem je surový plášť, ze kterého se hotový produkt vytvoří zvulkanizováním v lisu.
Složení gumárenských směsí
Suroviny a materiály používané pro výrobu směsí na jednotlivé konstrukční části významně ovlivňují jakost pneumatiky. Pouze z kvalitních surovin a materiálů lze vyrobit plášť pneumatiky, s jehož parametry lze docílit pohodlné a bezpečné jízdy vozidla s požadovanou životností pneumatiky.
Složení směsí používaných při výrobě plášťů patří mezi přísně střežená tajemství jednotlivých výrobců. Obecně se dá říci, že z materiálového hlediska objemově tvoří pneumatiku: 48% kaučuk, 36% přísad (technické saze a chemická aditiva), 16% výztužné materiály (kord a patní lana). Přesný podíl a druh jednotlivých složek, který bude tvořit gumárenskou směs, závisí v první řadě na tom, k jakému účelu, na jakých površích a za jakých podmínek bude budoucí pneumatika používána.
V praxi totiž neexistuje pryž, jejíž vlastnosti a adhezní schopnosti by byly ideální na všech površích a za všech podmínek. Proto vyrobit univerzální plášť pouze z hlediska složení směsi je úloha velice složitá. To, jakým způsobem ovlivní změna složení směsi změnu adhezních
schopností budoucí pneumatiky, závisí i na řadě dalších faktorů, kterými jsou druh materiálu druhého povrchu, po kterém se bude pneumatika pohybovat nebo velikost zatížení. Například zvětšování podílu sazí zvyšuje koeficient tření na abrazivním povrchu, ale na hladkém povrchu jej snižuje. Měkké směsi se obvykle vyznačují vyššími koeficienty tření než směsi tvrdší na hladkých površích, ovšem pouze při malém zatížení. Minerální oleje, které se přidávají do směsi, změkčují pryž, ale rostoucí stupeň zesítění pryže vznikající při vulkanizaci dělá pryž tvrdší a způsobuje její horší třecí vlastnosti.
Nejen pro různé typy, ale i pro výrobu jednoho pláště je potřeba hned několika druhů pryžové směsi. Konkrétní požadavky na vlastnosti pláště jsou zadávány na pracovišti výroby směsí, kde jsou připravovány jednotlivé druhy směsí s požadovanými vlastnostmi. V hnětacích strojích se vytvoří homogenní směs složená z požadovaného druhu kaučuku a aditiv, která potom putuje na jednotlivá dílčí pracoviště.
Kaučuky jsou makromolekulární látky, které patří mezi eleastomery. Eleastomer je látka, která se po deformaci vrací do původního stavu. V pneumatikárenském průmyslu se používá kaučuk jako základní složka pro výrobu pryže.
Přírodní kaučuk - získává se z kaučukodárných stromů a keřů, zejména druhu Hevea brasiliensis. Evropa se poprvé dověděla o zvláštní pružné hmotě od Kryštofa Kolumba po jeho cestě do Jižní Ameriky. Kaučukovníky se uměle pěstují na kaučukových plantážích v tropických pásmech Jižní Ameriky, jihovýchodní Asie a Afriky.
Po naříznutí kůry stromu vytéká bílá, mlékovitá kapalina zvaná latex, která obsahuje 30 – 40% koloidních částic kaučuku. Kaučuk se vysráží např. kyselinou mravenčí, vypere se vodou a suší se buď jen teplým vzduchem (bílá krepa – v pneumatikárenství používán jen omezeně), nebo dýmem (hnědá krepa, jinak též uzený kaučuk – v pneumatikárenství hojně používaný). Z jednoho stromu lze získat 5 - 25 kg kaučuku. Po chemické stránce je přírodní kaučuk polymer 2 - methyl -1,3 – butadienu - viz obrázek. Přírodní kaučuk se před vlastní přípravou směsi zpracovává tzv. lámáním. Příliš dlouhé řetězce se při něm štěpí účinkem vzdušného kyslíku v místě dvojných vazeb. K lámání dochází při průchodu kaučuku hnětacím zařízením. I když se dnes vyrábí desítky druhů různých syntetických kaučuků, přírodní kaučuk se používá stále, protože dodává směsím žádané vlastnosti. Navíc jeho cena je v současné době poměrně příznivá.
Vlastnosti přírodního kaučuku: malá odolnost vůči abrazi, malá odolnost vůči působení benzínu, oleje, petroleje a kyselin, snadno bobtná, podléhá rychlému stárnutí, výrazná lepivost.
Rozvoj automobilového průmyslu, s ním rostoucí spotřeba přírodního kaučuku na výrobu pneumatik a ne ve všech směrech ideální vlastnosti přírodního kaučuku přiměly chemiky k hledání odpovídající náhrady. Tou se stal syntetický kaučuk.
Syntetický kaučuk – je nepostradatelnou surovinou pro výrobu plášťů pneumatik. Jeho nepostradatelnost nevyplývá pouze z omezenosti zdrojů přírodního kaučuku, ale také z jeho mechanicko-fyzikálních vlastností, které umožňují jeho využití pro výrobu jednotlivých částí pláště pneumatiky. Oproti přírodnímu kaučuku je mnohem odolnější vůči nízké a vysoké teplotě a není citlivý na působení olejů.
K výrobě kaučukových směsí pro pláště osobních automobilů se využívají tyto syntetické kaučuky: butadienstyrenový kaučuk (SBR), butadienový kaučuk (BR), isoprenový kaučuk (IR).
Při výrobě materiálů pro pláště pneumatik se používají směsi přírodního a syntetického kaučuku pro dosažení lepších mechanicko-fyzikálních vlastností materiálu.
Přísady do kaučukových směsí
Ke zlepšení mechanických, fyzikálních a chemických vlastností směsí plášťů pneumatik, stejně jako k urychlení a zkvalitnění výrobního procesu, se do zpracovávaných kaučukových směsí dodávají přísady. Patří sem vulkanizační činidla, urychlovače a retardéry vulkanizace, aktivátory vulkanizace, ztužovala, antidegradanty, změkčovadla a ostatní přísady.
Saze - Používají se v pneumatikárenské výrobě jako plnivo ztužovadlo. Ve vyrobeném plášti jich bývá obsaženo okolo 27 objemových procent. Jejich pozitivní efekt spočívá v tom, že částice sazí jsou velmi jemné a v průběhu vulkanizace se dobře vážou s molekulami kaučuku. Po vulkanizaci kaučuku dodávají pryži pevnost a tvrdost, zvyšují odolnost proti opotřebení a zahřívání. Způsobují též tmavé zbarvení. Existuje několik druhů sazí. Pro výrobu plášťů pneumatik se používají saze retortové, které se získávají nedokonalým hořením par olejů ve speciálních pecích. Retortových sazí se vyrábí několik typů, které se liší svými vlastnostmi a vhodností pro použití na jednotlivé konstrukční části pláště. Množstvím a druhem použitých sazí se pomáhá dosahovat požadovaných vlastností běhounových směsí, směsí na výrobu bočnic, kostrových a nárazníkových směsí a ostatních směsí.
Silika - V současnosti probíhá hlavně u plášťů určených pro zimní provoz snaha nahrazovat saze sloučeninou na bázi oxidu křemičitého. Tato sloučenina je známá pod názvem silika. Výhodou směsi s vysokým obsahem siliky je, že začíná tvrdnout až při výrazně nižších teplotách než směs obsahující jako plnivo výhradně saze. Nahrazením sazí silikou je zabezpečeno zachování požadovaných adhezních schopností pneumatiky v zimních obdobích. Obsah sazí ku obsahu siliky je ve směsi použit v poměru od 3 : 2 do 1 : 9.
Antidegradanty - Konkrétně antioxidanty a antiozonanty mají velký vliv na zvýšení odolnosti pryže proti stárnutí. I po vulkanizaci zůstávají totiž v zesíťovaném polymeru ještě dvojné vazby, které jsou napadány kyslíkem a ozónem. Obsah ozónu ve vzduchu sice není velký, ale ozón je mnohem agresivnější než kyslík. Vznikají nestabilní peroxidy nebo ozonidy, které se radikálově štěpí a tak dochází k narušení struktury, což na pryži projevuje jako stárnutí. Proces napojování kyslíku a ozónu na dvojné vazby výrazně zpomalují látky zvané antioxidanty a antiozonanty. Mezi antidegradanty můžeme zařadit například substituovaný chinolin. Stárnutím ztrácí pryž třecí vlastnosti a následně pneumatika adhezní vlastnosti.
Do skupiny antidegradantů můžeme zařadit také ropné výrobky nazývané parafín. Jsou to směsi převážně tuhých parafinických uhlovodíků získané při odparafinování minerálních olejů. Po vulkanizaci vykvétá na povrchu pryže a vytváří jemnou ochrannou vrstvičku proti ozónovému stárnutí. Parafín chrání pryž pouze při skladování, jelikož při provozu je vykvetlý parafín z povrchu pneumatiky vlivem tření odstraněn.
Změkčovadla - Zvyšují plasticitu směsi, a usnadňují tak její mechanické zpracování. Po vulkanizaci ovlivňují tvrdost a tažnost vzniklé pryže. Jako změkčovadla se používají různé druhy minerálních olejů.
Pryskyřice - Přidávají se do některých kaučukových směsí pro zlepšení lepivosti směsi. Nejčastěji se používá kumaronová pryskyřice a kalafuna.
Vulkanizační činidla - Nejčastěji používaným činidlem je síra. Je to látka, v důsledku jejíž přítomnosti v kaučuku probíhá proces vulkanizace. V omezeném rozsahu se vulkanizuje také pomocí pryskyřic nebo pomocí organických peroxidů.
Ztužovadla - Tyto látky zvyšují tuhost a pevnost pryže. Patří sem saze, silika, síra.
Aktivátory vulkanizace - Nejčastěji užívaným aktivátorem vulkanizace, jejíž vulkanizát obsahuje síru, je oxid zinečnatý označovaný jako zinková běloba. Má významný vliv na tvorbu sítě. V důsledku jeho působení roste síťovací účinnost vulkanizace.
Urychlovače a retardéry vulkanizace - Dokážou výrazně zkrátit nebo prodloužit vulkanizační dobu směsi v souladu s výrobními požadavky.
Požadavky na směsi pro výrobu pláště pneumatiky
Běhounové směsi - vynikající odolnost proti otěru, pevnost v tahu, dobrá hystereze, odolnost proti stárnutí, dobrý koeficient tření s vozovkou. Složení běhounové směsi má rozhodující vliv na charakteristické vlastnosti pneumatiky.
Směsi pro potahování textilních kordů - vysoká tažnost, dobrý koeficient tření s viskózovými a polyamidovými kordy, odolnost proti tepelné únavě, odolnost proti stárnutí.
Směsi pro potahování ocelových kordů - Mají shodné vlastnosti jako směsi pro textilní kordy. Nejčastěji se zde používá směs s velkým množstvím přírodního kaučuku, jehož schopnost pevného spojení s ocelovým kordem je vyšší než u syntetických kaučuků.
Směsi pro obstřik patních lan - velmi dobré třecí schopnosti s ocelovým lankem a s ostatními částmi patky pláště.
Směsi na výrobu bočnic - dobrá odolnost proti stárnutí, odolnost proti vzniku a růstu trhlin. V oblasti ochranného patního pásku se musí zvulkanizovaná směs vyznačovat vysokými adhezními schopnostmi k materiálu ráfku kola.
Výztužné materiály
Vlastnosti materiálu, ze kterého je plášť vyroben, nejsou závislé pouze na vlastnostech pryže vznikající při vulkanizaci, nýbrž na interakci vlastností pryže a výztužných materiálů. Spojením na první pohled nesourodých složek vzniká při vulkanizaci typ vláknového kompozitu. Vlastnosti vzniklého kompozitu jsou kombinací tuhosti a pevnosti vláken výztužných materiálů a pružnosti matrice (pryže). Směrem uložení vláken je možno zvyšovat pružnost vzniklého materiálu v požadovaném směru. Pro jednotlivé konstrukční části pláště jsou používány rozdílné typy výztužných materiálů v závislosti na požadavcích na jejich mechanicko-fyzikální vlastnosti.
Výztužné materiály se v pneumatikárenství nazývají souhrnně kordy.
Aby kompozit vzniklý spojením výztužných materiálů a pryže plnil správně svoji funkci, musí být zabezpečena dostatečná soudržnost povrchu kordů a pryže. Pro zlepšení soudržnosti se buď kordy impregnují speciálními látkami, které zvyšují koeficient tření mezi oběma povrchy, nebo je látka s podobným účinkem přidávána přímo do kaučukové směsi. První možnosti se využívá u textilních kordů (viskózových, polyamidových, polyesterových a skleněných). Druhá metoda je vhodná pro ocelové kordy.
Ocelové kordy - Jsou používány díky jejich vysoké pevnosti a rozměrové stabilitě. Musí být odolné vůči korozi a klást dostatečný odpor proti pohybu. Ocelové kordy jsou vyrobeny z drátů, které jsou pomosazené (70 % Cu a 30 % Zn). Mosazná vrstvička na povrchu drátu má schopnost vytvořit lepší třecí vlastnosti mezi kovem a pryží.
Textilní kordy - Obdobně jako ocelové kordy dávají textilní kordy plášti pevnost a rozměrovou stabilitu. Jsou však lehčí a některé z nich jsou snadno deformovatelné ohybovým zatížením. Mezi textilní kordy patří viskózová, skleněná, polyesterová a polyamidová vlákna.
V současnosti se začínají používat aromatická polyamidová vlákna s lepšími materiálovými vlastnostmi a menší hmotností. Tato vlákna jsou známa pod názvem kevlarová vlákna.
Výrobní postupy
Pogumování kordu - Kordy jsou vlákna z ocele, hedvábí, polyesteru, polyamidu nebo kevlaru, která plní v pneumatice velmi důležitou roli z hlediska její pevnosti. Tvoří základ kostry i nárazníku. Uvnitř pláště musejí být jednotlivá vlákna od sebe oddělena pryžovou směsí, aby se vzájemně o sebe netřela. Vzájemné tření by totiž bylo příčinou narušení struktury vláken a následně přetržení vlákna, což by vedlo ke ztrátě pevnosti materiálu pneumatiky.
Na pracovišti gumování kordu je tedy tkanina opatřována vrstvou pryže. Podle potřeby se dále zpracovává – pro výrobu radiálních plášťů je třeba změnit orientaci kordových vláken, proto se z cca 1,5m širokého pásu pogumovaného kordu řežou jednotlivé dílce požadované šíře, které se kladou za sebe a spojují. Tím se získá výchozí materiál pro výrobu kostry radiálního pláště.
Příprava běhounů a bočnic - Běhouny jsou složeny z několika typů pryže. Vrchní část, tedy ta, která je ve styku s vozovkou, má vlastnosti odpovídající požadavkům na schopnosti běhounu. Pod ní se nachází tenká vrstvička základní, tzv. base směsi s podílem sazí, jejíž materiální složení ovlivňuje i některé vlastnosti vrchní části běhounu. Mezi tyto vlastnosti patří zejména tvrdost bloků běhounu vůči ohybu vznikajícím působením třecích sil. Okrajové části běhounového pásu jsou pak tvořeny bočnicovou směsí.
Samotná bočnice je však vyrobena rovněž ze dvou druhů směsi. Zatímco její vnější část, tedy ta blíže k dezénu, je vyrobena z pružnější směsi, oblast blíže u patky je vyrobena z tužší směsi, která patku lépe chrání.
V obou uvedených případech, u běhounové i patkové pryže, jsou jednotlivé vrstvy skládány tak, aby se vlastnosti pryže v plášti měnily plynule z hlediska pružnosti a tvrdosti.
Výroba nárazníku - Další část pláště, která se připravuje samostatně, je nárazník. Jeho konkrétní konstrukce se samozřejmě opět liší podle typu pláště, ovšem obecně je tvořen pásem ze vzájemně překřížených pogumovaných ocelových kordů, uložených pod určitým úhlem. U vysokovýkonných plášťů se mezi běhounem a nárazníkovým pásem používá další nárazníková vrstva z polyamidového pogumovaného kordu, který se dříve pokládal jako prstenec z pásu, a tak v jednom místě vznikl spoj po celé šířce pláště. Dnes se nárazníková vrstva tvoří tak, že se na prstenec ocelového kordu navíjí ve spirále pásek polyamidového kordu. Tak vznikne nárazníková vrstva polyamidového kordu bez spoje.
Výroba patních lan - Vytváří se prstenec se čtyřmi pogumovanými ocelovými lanky vedle sebe. Tento prstenec se následně rozdělí na čtyři jednotlivá lana. Naráz se tak vyrábějí patní lanka vždy pro dva pláště.
Kompletace (konfekce) - Výroba surového pláště probíhá ve dvou stupních. V prvním stupni se na vnitřní gumu nalepí kordová vložka. Z boku se potom narazí patní lana a kordová vložka se přehne přes lano. Následně se položí bočnice.
Ve druhém stupni se připravuje nárazníkový prstenec s běhounem. Na vrstvu pogumovaného ocelového kordu kostry se položí polyamidový nárazník a běhoun.
Při vlastní konfekci se potom obě části spojí dohromady a zaválejí. Tak vznikne surový plášť.
Vulkanizace - Vulkanizace je fyzikálně – chemický proces, při kterém se za působení teploty, tlaku a vulkanizačního činidla mění struktura kaučukové směsi. Kaučuk s lineární strukturou makromolekul se mění v pryž s prostorovou strukturou makromolekul. Během vulkanizace se mezi lineárními řetězci tvoří příčné vazby, které způsobí zesíťování struktury látky.
Podle použitého vulkanizačního činidla mohou být příčné vazby tvořeny buď jednoduchou chemickou vazbou (např. vazbou mezi atomy uhlíku jednotlivých řetězců nebo jedním ale i více atomy síry), nebo např. řetězci fenolformaldehydové pryskyřice. Vlastnosti vulkanizátu jsou závislé na koncentraci příčných vazeb, pravidelnosti jejich rozložení a na jejich stabilitě. Stabilita příčných vazeb se mění podle toho, mezi jakými prvky je vazba vytvořena.
Hlavním důvodem, proč se kaučuk vulkanizuje je, že se podstatně vylepší jeho mechanické i fyzikálně - chemické vlastnosti. Z mechanických vlastností se zvýší pevnost v tahu, strukturní pevnost (odolnost proti dalšímu trhání), odolnost v oděru i pružnost, ale zároveň se sníží tažnost. Na rozdíl od nevulkanizovaného kaučuku, který je rozpustný v některých organických rozpouštědlech, vulkanizovaný kaučuk v nich jen bobtná. Vulkanizovaný kaučuk je také méně citlivý ke změnám teploty a zachovává si ohebnost i tuhost ve značném teplotním rozsahu.
Z hlediska pracovních úkonů probíhá vulkanizace tak, že se surový plášť vloží do lisovací formy (vulkanizačního lisu), která nese podobu budoucího pláště, tedy otisk dezénu a veškerého označení. Působením horké tlakové páry o teplotě v rozmezí 140 - 180o Cse polotovar vytvaruje podle formy a zároveň působením vulkanizačního činidla kaučuk zvulkanizuje. To znamená, že tváření výrobku a vulkanizace jsou spojeny v jednu operaci. Aby se výrobek na formu nepřilepil, vystřikuje se forma emulzemi separačních činidel. Vulkanizace probíhá po dobu 7 až 11 minut, podle rozměru pláště.
Zkoušení pneumatik ve výrobním závodě
Kontrola a zkoušení pneumatik - Po zvulkanizování se všechny pláště dopraví na pracoviště kontroly a následně do skladu. Protože se vyrábí současně asi 150 různých provedení plášťů ( kombinace rozměrů a typů dezénu ), ještě u lisu jsou opatřeny čárovým kódem tak, aby byla zlepšena jejich identifikace.
Vlastní kontrola kvality je několikastupňová. To znamená, že všechny pláště jsou podrobeny vizuální výstupní kontrole a tzv. testu uniformity. Z produkce se pak náhodně vybírají vzorky pro podrobnější testování.
Ale i po bezchybném splnění všech výše popsaných kontrol a zkoušek není ještě zaručeno excelentní chování pneumatiky po obutí na disk automobilu. Nejvhodnějším způsobem zjišťování kvality a životnosti pneumatiky je zkouška v podmínkách budoucího využití tohoto výrobku v praxi. Takovéto zkoušky nazýváme souhrnně silniční zkoušky.
Test uniformity - V první fázi se plášť nasadí na ráfek a nahustí na 0,4 MPa, aby řádně dosedl. Současně se pomocí snímačů provádí testování boulí a propadlin. Pak se tlak sníží na 0,2 MPa a pneumatika se přitlačí na pružně uložený válec a roztočí se. Uložení válce je osazeno snímači snímajícími sílu, kterou plášť na válec působí. Protože plášť není stejně tuhý po celém obvodu, síla se mění a toto kolísání síly je jednou z hodnocených veličin. Podle změny velikosti působící proměnné síly v čase se zjišťuje rozdíl mezi maximální a minimální výchylkou radiální síly. Další čidlo, kterým je otáčející se zkušební válec osazen, zachycuje kolísání boční (axiální) síly. Totiž plášť, jehož nárazník není umístěn přesně uprostřed, se při otáčení začne deformovat do tvaru kužele a začne vyvozovat boční sílu. Kolísání boční síly je potom dalším z hodnotících parametrů. Pláště pro první vybavení se podle požadavků zákazníka na té straně, která vykazuje kladný nebo záporný kónusový účinek, označují tečkou a výrobce vozu pak montuje na nápravu pneumatiky tak, aby se tento u obou kol navzájem eliminoval.
Podrobnější testování náhodně vybraných vzorků - K testům, které se provádějí namátkově u předepsaného vzorku produkce, patří např. test ocelových nárazníků na rentgenu a následná vizuální kontrola. Vizuální kontrola u náhodně vybraného vzorku je mnohem podrobnější než vizuální kontrola prováděná sériově u každé pneumatiky. Velmi důležitá je kontrola řezu pláště, kdy se vybere vzorek pláště, rozřeže a podle podrobné metodiky se přesně měří všechny rozměry a parametry, jako jsou tloušťka bočnice, zakotvení, uložení nárazníku, hmotnost atd.
Pokud je určitý typ pláště vyráběn pro předem určený typ vozu, každý výrobce vozu pak specifikuje svoje požadavky např. tím, že stanoví přípustné tolerance jednotlivých veličin.
Valeni kola s pneumatikou po vozovce
Každé kolové vozidlo, tedy i osobní automobil, se prostřednictvím kol s pneumatikou stýká s vozovkou nebo s povrchem, po kterém se pohybuje. Kola s pneumatikou (dále jen pneumatiky) mají při tom za úkol přenášet všechny síly vycházející z vozidla na vozovku a naopak síly vycházející z vozovky na vozidlo. Pneumatika proto musí plnit následující funkce:
-
přenášet svislé síly mezi kolem a vozovkou, tečné síly a boční síly. Svislé síly jsou představovány tíhou vozidla, tečné síly vznikají při akceleraci a brzdění vozidla a boční síly vznikají při jízdě v důsledku nutnosti vedení vozidla.
-
umožnit pohyb vozidla v důsledku valení
-
tvořit součást pérování vozidla svou pružností
Úkol pneumatiky
Pneumatika plní na kole automobilu výše zmíněné funkce. Při plnění těchto funkcí musí pneumatika zajistit, aby jízda automobilu byla ve všech jízdních režimech co nejbezpečnější a co nejpříjemnější pro řidiče automobilu a posádku. Jízdními režimy rozumíme akceleraci, brzdění a volnou jízdu automobilu po vodorovné, klesající nebo stoupající vozovce při různých klimatických a povětrnostních podmínkách, dále pak jízdu zatáčkou buď v případě, kdy vozidlo projíždí zatáčkou bez brzdění či akcelerace, nebo v případě, že vozidlo zrychluje či zpomaluje. Průjezd zatáčkou musí být co nejbezpečnější také ve všech klimatických podmínkách. Pneumatika na kole automobilu se musí také snažit zajistit co nejstabilnější chování vozidla při náhlém natočení volantu a vybočení rejdových kol automobilu z přímého směru. Pneumatika musí zajistit dobrý tlumící efekt při přejezdu kol přes nerovnosti, ale nesmí při tom dopustit vznik ztráty nebo nedostatečného kontaktu pneumatiky s povrchem vozovky. Aby došlo ke splnění těchto požadavků, musí pneumatika: mít schopnost nést určitou zátěž, bez výrazné deformace; mít schopnost tlumit nárazy; přenášet hnací a brzdné síly; vyvíjet boční síly; vyznačovat se dobrou adhezí k vozovce za různých podmínek; být rozměrově stabilní; mít určitou životnost; dobře reagovat na řízení; klást minimální valivý odpor; vyvíjet co nejméně hluku a vibrací; mít minimální hmotnost.
Vlastnosti kola s pneumatikou
Pneumatika automobilu je pružná ve třech základních směrech
Radiální pružnost pneumatiky
Je to pružnost v rovině kolmé na vozovku. Tato pružnost se významně podílí na pérování vozidla. Velikost radiální pružnosti pneumatiky je vyjádřena radiální tuhostí pneumatiky. Radiální tuhost pneumatiky je možné vypočítat jako poměr radiálního zatížení kola ku radiální deformaci kola. Průběh radiální deformace je mírně progresivní, což je z hlediska odpérování automobilu velmi výhodné. Radiální pružnost pneumatiky je dána její konstrukcí a předpětím stěn pláště, které vzniklo v důsledku tlaku nahuštěného vzduchu uvnitř pneumatiky.
Obvodová pružnost pneumatiky
Obvodová pružnost se projevuje při zatížení kola momentem nebo obvodovou silou. Pokud přivedeme na kolo automobilu stojícího na vozovce kroutící moment, dojde k pootočení ráfku kola vůči vozovce o úhel, aniž by při tom došlo k pootočení pneumatiky. Závislost momentu na úhlu pootočení nazýváme obvodová deformační charakteristika pneumatiky. Pootočení ráfku je způsobeno nakrucováním kostry pneumatiky a deformací výstupků běhounu. Při menších hodnotách zatěžování je deformační charakteristika přibližně lineární a obvodová tuhost pneumatiky se dá vypočítat jako poměr kroutícího momentu přivedeného na kolo a úhlu pootočení ráfku. Obvodová tuhost závisí především na konstrukci pneumatiky. Obvodová pružnost zmírňuje rázy v; převodovém ústrojí, a tím zvyšuje trvanlivost ozubených kol a ložisek automobilu. Nepříznivě se však projevuje na prokluzování kol, a tím i na opotřebení běhounu pneuatik.
Boční pružnost pneumatiky
Díky boční pružnosti pneumatiky a díky axiálnímu (bočnímu) zatížení kola silou může dojít například při jízdě zatáčkou k posunutí středu kola. Vzájemná závislost působící boční síly a velikosti vybočení středu kola nazýváme boční deformační charakteristikou pneumatiky. Vybočování středu kola je způsobeno deformací kostry pláště a deformací běhounu. Boční tuhost pneumatiky je kromě konstrukce pneumatiky závislá také na jejím nahuštění. Se zvyšujícím se tlakem uvnitř pneumatiky se zvyšuje její boční tuhost. Pružnost pneumatiky v bočním směru je nežádoucí, protože jejím důsledkem dochází k vybočování vozidla ze směru určeném natočením kol, a tím zhoršuje směrovou stabilitu a řiditelnost vozidla.
Princip přenosu sil ve styku kola s vozovkou
Kolo s pneumatikou je část automobilu, jejíž hlavní funkcí je přeměnit rotační pohyb vycházející u motorových dopravních prostředků z klikového hřídele motoru na pohyb, který posunuje dopravní prostředek po vodorovné ose. Tento pohyb nazýváme pohybem posuvným. Posuvný pohyb je realizován v důsledku vzniku tečné síly FT ve styčné ploše pneumatiky s vozovkou.
Přenos tečné síly mezi kolem a vozovkou je umožněn třením pryže pneumatiky o vozovku, zachytáváním běhounu o mikronerovnosti vozovky, zachytáváním o makronerovnosti vozovky účelně vytvořenými výstupky běhounu a přisáváním běhounu k vozovce.
Částice běhounu přicházejí do styku s vozovkou nezatížené tečnou silou, a tím pádem v nedeformovaném stavu. V okamžiku dotyku části běhounu s vozovkou je tečná deformace této části nulová, ale při průběhu části styčnou plochou se postupně zvětšuje. Tečná deformace částí běhounu se ve styčné ploše pneumatiky s vozovkou postupně zvětšuje díky narůstajícím tečným silám. Body A, B, C, D a E jsou místa ve stopě pneumatiky, ve kterých jsou naznačeny tečné deformace dxA, dxB dxC dxD dxE . Až do bodu D tečná deformace narůstá. Tečná deformace může narůstat, dokud není porušena soudržnost pneumatiky s vozovkou. V bodě D a E dochází k porušení soudržnosti, a proto tečná deformace zůstává konstantní. K deformaci běhounu může docházet, jelikož je pneumatika obvodově pružná. Velikost tečné síly, která vzniká ve styčné ploše pneumatiky s vozovkou, je omezena adhezní silou Fad.
Velikost adhezní síly nám udává maximální možnou velikost tečné síly, kterou je schopno kolo přenést při určitém radiálním zatížení pneumatiky. Velikost adhezní síly je možno vyčíslit jako součin radiálního zatížení pneumatiky a součinitele adheze. Zpravidla bývá maximální hodnota součinitele adheze pneumatiky dosahována při 15 – 30 % skluzu pneumatiky. O velikosti součinitele adheze při určitém skluzu pneumatiky nám vypovídá skluzová charakteristika pneumatiky. Skluzovou charakteristiku můžeme graficky znázornit jako závislost skluzu pneumatiky na součiniteli adheze pneumatiky.
Faktory ovlivňující velikost adhezní síly
Adhezní síla, kterou je schopno vozidlo přenášet buď při brzdění, při akceleraci nebo při jízdě zatáčkou, závisí, jednak na radiálním zatížení pneumatik, které se na přenosu sil podílejí a jednak na velikosti součinitele adheze, který je na těchto pneumatikách jedoucích na dané vozovce za daných podmínek.
Při akceleraci vozidla se velikost adhezní síly určuje jako součin zatížení poháněných kol a součinitele adheze těchto kol. Kola, která nejsou poháněná, nemají na velikost adhezní síly vozidla při akceleraci žádný vliv. Při jízdě vozidla po vozovce, která není vodorovná, je pro výpočet adhezní síly nutno uvažovat zatížení kol působící ve směru kolmém k vozovce.
Při brzdění vozidla představuje celkovou adhezní sílu vozidla součin zatížení všech brzdících kol se součinitelem adheze těchto kol. Kola, která nejsou brzděná, nemohou přenášet brzdný moment, a proto nemají na adhezní sílu vozidla při brzdění žádný vliv. Stejně jako v případě akcelerujícího vozidla je při jízdě do stoupání nebo do klesání nutné počítat se zatížením kol působícím ve směru kolmém k vozovce.
Při jízdě vozidla zatáčkou se na přenosu adhezní síly podílejí všechna kola, která jsou ve styku s vozovkou. Při výpočtu adhezní síly počítáme s radiálním zatížením všech kol společně s jejich adhezními součiniteli. Pokud vozidlo zatáčí na vozovce do stoupání nebo klesání, je nutné i v tomto případě počítat se zatížením kolmým k vozovce.
Součinitel adheze pneumatiky je konstanta nezávisející na pouhém tření pryže vzorku pneumatiky o povrch vozovky. Velikost součinitele adheze je větší než součinitel tření pryže pneumatiky o vozovku. Při rotačním pohybu pneumatiky po vozovce a při přenosu hnací síly dochází totiž navíc k zachytávání hranek vzorku o mikronerovnosti vozovky. Součinitel adheze je závislý na druhu a stavu povrchu vozovky, vlastnostech povrchu pneumatiky, měrném tlaku mezi kolem a povrchem a rychlosti jízdy vozidla.
Součinitel adheze = součinitel tření pryže pneumatiky + součinitel míry zachytávání hran vzorku o mikronerovnosti vozovky
Vliv povrchu vozovky na součinitel adheze
Povrch vozovky je v praxi z hlediska bezpečnosti silničního provozu nejvýznamnějším činitelem změny součinitele adheze. Vlastnosti povrchu vozovky se totiž během jízdy automobilu průběžně mění v závislosti na stáří vozovky, materiálu, ze kterého je svrchní část vozovky vyrobena, na znečištění vozovky a na klimatických podmínkách. Posoudit součinitel adheze vozovky je z pohledu řidiče automobilu během jízdy mnohdy značně složitý úkol a často i úkol neproveditelný. Obecně platí, že na pozemních komunikacích je možno dosahovat součinitele adheze v rozmezí od 0,1 na náledí do 1,0 na suchém betonu. Ve výjimečných případech je možné dosahovat součinitele adheze větší než 1. Na suché vozovce budeme dosahovat vyššího součinitele adheze než na vozovce mokré. Na čisté vozovce budeme dosahovat vyššího součinitele adheze než na vozovce zablácené. Přehled průměrných hodnot součinitele adheze na různých površích je zobrazen v tabulce. V praxi může nastat situace, při níž dojde k náhlému a výraznému poklesu součinitele adheze, a to v okamžiku začátku deště a v okamžicích bezprostředně po začátku deště. Tento jev se nejvíce projevuje na asfaltové vozovce nebo na vozovce z žulové dlažby. V tomto případě dojde náhle k poklesu součinitele adheze z 0,8 až na 0,3. Náhlý pokles součinitele adheze vzniká v důsledku vytvoření tenké vrstvičky bláta z nečistot na vozovce. Bláto se po určité době smyje a na vozovce vzniká situace mokrého asfaltu se součinitelem adheze dosahující hodnoty přibližně 0,5.
Vliv vlastností povrchu pneumatiky na součinitel adheze
Povrch pneumatiky, zejména pak její běhoun, je jedinou částí pneumatiky, na které přímo závisí součinitel adheze pneumatiky na daném povrchu. Při navrhování a konstrukci běhounu a vzorku běhounu pneumatiky se musí dbát na to, aby pneumatika dosahovala co nejlepších adhezních vlastností na všech typech a druzích povrchů, pro které je pneumatika určena. Úkol, navrhnout takovouto univerzální pneumatiku, není úkolem snadným, protože vlastnosti pneumatiky závisí na řadě protichůdných způsobů konstrukčních řešení.
Vliv tvaru vzorku - tvar vzorku společně se složením směsi, ze které je vzorek vyroben, má z pozice pneumatiky bezpochyby největší vliv na adhezní součinitel pneumatiky. Z hlediska účelu, pro který je pneumatika určena, rozeznáváme tři základní typy vzorků běhounu. Pásový lamelový vzorek (Obr. a) je vhodný pro používání při jízdě na silnici. Vzorek je totiž uspořádán tak, aby hrany segmentů vzorku dokázaly zachytávat o mikronerovnosti vozovky jak v podélném, tak i v příčném směru, přičemž drážky mezi segmenty vzorku jsou poměrně úzké. Typickým znakem pásového lamelového vzorku je velký počet segmentů dezénu. Při růstu počtu segmentů přímo úměrně totiž roste počet hran, které zachytávají o mikronerovnosti vozovky, a tím se zvyšuje součinitel adheze pneumatiky. Poměrně malá rozteč drážek ve vzorku vychází z potřeby silničního pláště dosednout co největší plochou hmoty vzorku na vozovku, avšak tento požadavek značně znemožňuje použití silniční pneumatiky v terénu. V terénu by totiž došlo k zanesení úzkých drážek nečistotami, a tím by se anuloval jeden z faktorů součinitele adheze, a to zachytávání hran vzorku o nerovnosti vozovky. Přilnavost pneumatiky by byla odkázána pouze na prosté tření, jehož součinitel v terénu je velice malý.
Pásový vzorek (Obr. b) má v důsledku vzorku pouze s obvodovými drážkami velikou schopnost přenášet boční síly. Jeho schopnost přenášet hnací nebo brzdné síly je ve srovnání s pásovým lamelovým vzorkem malá, jelikož postrádá hranky dezénu, které by byly schopné při akceleraci nebo brzdění zachytávat o mikronerovnosti vozovky. Tento vzorek je z toho důvodu vhodný pro nepoháněná a nebrzděná kola.
Šípový vzorek (Obr. c) je typický vzorek vhodný při jízdě v terénu. Segmenty jeho vzorku jsou přizpůsobeny pro přenos hnacích, brzdných i bočních sil. Základem přenosu sil je u této pneumatiky boření pneumatiky do určité hloubky a zachytávání segmentů vzorku o segmenty nezhutněného terénu vzniklé bořením pneumatiky. Drážky mezi segmenty vzorku jsou velice široké a navíc jsou umístěny tak, že pneumatika má tzv. samočisticí efekt. Samočisticí efekt je vlastnost, díky které pneumatika při jízdě terénem vytlačuje nečistoty a zbytky nezhutněné vozovky ven ze vzorku pneumatiky a nedochází tak k zanesení drážek dezénu. Pneumatiku se šípovým vzorkem je možné použít i při jízdě na zpevněné vozovce, ale pneumatika nebude dosahovat takových adhezních vlastností jako pneumatika s pásovým vzorkem. Důvodem je malý počet hran dezénu schopných zachytávat o mikronerovnosti vozovky. Pneumatika s šípovým vzorkem bude navíc na zpevněné vozovce trpět zvýšenou hlučností a segmenty vzorku budou podléhat rychlejšímu opotřebení. Výhodou pneumatiky s šípovým vzorkem na zpevněné vozovce bude vysoká odolnost pneumatiky proti vzniku akvaplaninku.

Vliv výšky vzorku běhounu – výška vzorku běhounu ovlivňuje součinitel adheze, a tím i jízdní stabilitu vozidla zejména na vozovce s určitou vrstvou vodního filmu. Součinitel adheze na mokré vozovce klesá se zvyšující se obvodovou rychlostí kola tím prudčeji, čím nižší je vzorek běhounu pneumatiky. Na obrázku je graficky znázorněna tato závislost při jízdě pneumatiky osobního automobilu na vozovce s výškou vodního filmu 2-3 mm. Tato závislost je zapříčiněna zaprvé tím, že při zvětšování obvodové rychlosti pneumatiky se zkracuje čas, který mají drážky vzorku běhounu pneumatiky na to, aby odvedly požadované množství kapaliny z prostoru pod pneumatikou, což je příčinou klesající tendence křivky a za druhé tím, že zmenšování výšky vzorku zmenšuje drážkový prostor vzorku, a tím pádem už menší objem kapaliny na vozovce naplní drážku vzorku a proces vytláčení kapaliny musí začít dříve, resp. při nižší výšce kapalinového filmu, než u vzorku vyššího. Kapalina, která není odvedena mimo stykovou plochu pneumatiky s vozovkou, je zdrojem síly, která působí proti tíze vozidla, a tím znemožňuje přenos maximální adhezní síly vozidla. Pneumatika je jakoby odtlačena tlakovou silou kapaliny od vozovky. Při úplném odtlačení pneumatiky, tzn. v situaci, kdy tlaková síla kapaliny překoná tíhu vozidla, dojde k situaci, při které se styk kola s vozovkou uskutečňuje pouze přes vrstvu kapaliny. V takové situaci prudce klesne hodnota součinitele adheze až na 0,001. Tento jev se nazývá
akvaplanink. Informace o závislosti brzdné dráhy na výšce profilu jsou uvedeny v sekci
užitečné informace.
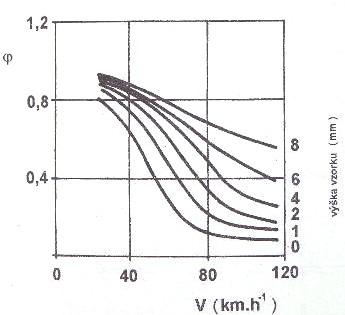
Další výhoda běhounu s velkou výškou vzorku je oproti běhounu s malou výškou v tom, že dosahuje většího součinitele adheze na kluzkých vozovkách. Jak už bylo popsáno výše, součinitel adheze závisí na součiniteli tření pryže, ale zároveň na zachytávání hranek vzorku o mikronerovnosti vozovky. Čím kratší je pryžový výstupek vzorku, tím je potřeba větší tečná síla k tomu, aby jej zdeformovala v obvodovém směru a natočila jeho hranku tak, aby mohla co nejúčinněji zachytávat o mikronerovnosti vozovky. Na kluzkých vozovkách je vznik těchto tečných sil omezený.
Vliv materiálu vzorku běhounu – vlastnosti materiálu, ze kterého je vzorek běhounu vyroben, mimo jiné určují, jakým způsobem bude povrch pneumatiky reagovat na změnu teploty prostředí, ve kterém se pneumatika pohybuje. Obecně se s rostoucí teplotou prostředí zvyšuje teplota pryže, ze které je běhoun vyroben a pryž se stává plastičtější. Při zvyšování plasticity pryže sice dochází ke zlepšování adhezních podmínek ve stopě, ale současně se běhoun pneumatiky stává náchylnější k opotřebení. Další nevýhodou nadměrně plastického běhounu pneumatiky je skutečnost, že změkčením běhounu pneumatiky dojde ke zvýšení pružnosti pneumatiky v axiálním (bočním) směru, jejíž působení jsme si již v předchozích kapitolách označili jako nežádoucí. Proto je potřebné volit pro výrobu běhounu pneumatiky druh pryže vhodný pro určité teplotní podmínky. Změna přilnavosti pneumatik s měnící se teplotou je zobrazena u zimního a letního běhounu v sekci užitečné informace. Ideální materiál pro výrobu vzorku běhounu by byl materiál absolutně tuhý v axiálním směru, současně ale dostatečně pružný při přenosu sil působících na pneumatiku v obvodovém směru, aby dokázal tlumit rázy přicházející do hnacího a brzdného ústrojí při akceleraci a brzdění a aby umožnil zachytávání hranek vzorku o mikronerovnosti vozovky. Materiál by musel být pružný při radiálním zatížení pneumatiky, aby dokázal tlumit rázy vzniklé při jízdě přes nerovnosti na vozovce. Dostatečná pevnost materiálu by zajišťovala nízkou míru opotřebení, avšak současně by musel materiál vykazovat vynikající přilnavost k vozovce (přilepování na vozovku), která je podmíněna dostatečnou plasticitou materiálu. Všechny tyto vlastnosti by si musel ideální materiál zachovat při všech teplotních podmínkách, které se při provozu vozidla vyskytují.
Z uvedených požadavků je zřejmé, že nároky kladené na materiál jsou vysoké, v některých hlediscích protichůdné a místy i z materiálového hlediska nerealizovatelné. Proto při výrobě běhounu musí docházet k určitým kompromisům a vznikají pneumatiky se specializací na různé povrchy, styly jízdy a teplotní podmínky.
Vliv měrného tlaku ve stopě na součinitel adheze - měrný tlak ve stopě vzniká v důsledku působení zatížení kola na styčnou plochu pneumatiky s vozovkou. Z obecné rovnice pro výpočet tlaku, kde p=F/S, vyplývá, že čím je větší styčná plocha pneumatiky s vozovkou, tím je měrný tlak ve stopě menší. Velikost styčné plochy je u jednoho typu pneumatiky proměnná veličina, jelikož je ovlivnitelná tlakem huštění pneumatiky. Čím větší je tlak huštění pneumatiky, tím je styčná plocha mezi pneumatikou a vozovkou menší. Proto můžeme tvrdit, že měrný tlak je funkcí zatížení pneumatiky a jejího huštění. Standardně jsou pneumatiky huštěny atmosférickým vzduchem. V současnosti se ale stává populární huštění pneumatiky směsí dusíku a argonu. Tato směs má řadu vhodných vlastností, jako napříkla teplotní objemovou stálost. Na obrázku 1 je zobrazena závislost součinitele adheze na zatížení a huštění pneumatiky na ráfku 8,25 - 20. Z obrázku je patrné, že se zmenšujícím se tlakem huštění pneumatiky při určitém zatížení roste součinitel adheze. Závislost růstu součinitele adheze na zmenšování tlaku huštění v pneumatikách platí pouze do určité hodnoty tlaku. Po poklesu tlaku huštění pod tuto mezní hodnotu začne součinitel adheze pneumatiky klesat, jelikož vzorek běhounu přestává plnit svou funkci zachytávání hranek vzorku o mikronerovnosti vozovky a styčná plocha pneumatiky s vozovkou se začíná deformovat (obrázek 2). Vzorek běhounu je v určitých místech nařezán tak, že vznikají lamely. Ty se při akceleraci a styku s vozovkou od sebe rozevřou, a tím obohacují vzorek o další přídavné hrany potřebné pro lepší adhezní vlastnosti pneumatiky. Pokud není pneumatika dostatečně nahuštěná, lamely neplní svoji funkci. Vliv tlaku huštění na některé jízdní vlastnosti vozu je popsán v sekci užitečné informace.
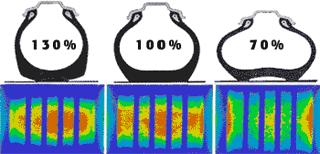
Vliv rychlosti jízdy na součinitel adheze - Rychlost jízdy vozidla nebo přesněji obvodová rychlost částic vzorku běhounu ovlivňuje velikost součinitele adheze. Pravidlo, že při vzrůstající rychlosti jízdy klesá součinitel adheze, neplatí pouze při jízdě po vozovce s určitou vrstvou kapaliny, jak bylo uvedeno v části věnované výšce vzorku běhounu, ale platí i pro odvalování pneumatiky po suchém povrchu. Když se zvětšuje rychlost rotace pneumatiky, běhoun nemá dostatečně dlouhou dobu na dokonalé přilnutí k povrchu vozovky a jednotlivé hranky vzorku běhounu ideálně nezachytávají o mikronerovnosti vozovky. Podobně je degradována i funkce přilepování povrchu běhounu k povrchu vozovky. Závislost součinitele adheze na rychlosti jízdy na suchém povrchu je uvedena na obrázku. Závislost délky brzdné dráhy na různých rychlostech a druzích povrchů je možné najít v sekci
užitečné informace.
www.pneu-asistent.cz - Váš průvodce světem pneumatik - www.pneu-asistent.cz
Vaše bezpečnost je naším cílem